Making a Difference
At BioFire, we make a difference, we make the world a healthier and better place. We provide molecular solutions that lessen the time to medical results, empower healthcare professionals to make better diagnostic decisions and lower healthcare costs. We are committed to improving the quality of life for everyone, everywhere, every day.
We surround ourselves with world-class individuals and are committed to a set of principles to build a thriving organization and foster a vibrant community based on trust, integrity and a shared sense of purpose. We reinforce each other’s discipline, creativity and sense of the possible in an exciting environment that is characterized by mutual respect and challenging and fulfilling activity. The diligent and interdependent work of every individual is what makes BioFire exceptional.
Top 10 Reasons to Work at BioFire
There’s a lot to love about working at BioFire. Here are the top 10 things our employees say that they like the most:
- Contributing to work that saves lives and makes the world a healthier place
- Schedules and benefits that emphasize a healthy work/life balance – including at least 4 weeks of paid time off each year!
- Exceptional health and wellness benefits with a generous 401k plan with no vesting period
- Great pay and annual discretionary bonuses
- Culture of appreciation and recognition
- Challenging work with career growth opportunities
- Great management who implement employee ideas and rewards hard work
- Opportunities to learn new things and gain new skills, including tuition reimbursement
- Fun company events
- Casual working environment that feels like a home away from home
Career Opportunities
BioFire offers a broad range of positions in various departments. We look for talented individuals to fill roles in manufacturing, engineering, sales and marketing, R&D, software development and many other departments. We offer competitive salaries, vacation and holiday pay, 401(k), medical benefits and an invigorating work environment.
We believe in our team members and encourage them to excel in their fields. If you are resourceful, think outside of the box and are passionate about what you do, apply for a position below.
Featured Jobs
Find Jobs
Business Support
Engineering
Associate Principal Software Engineer | Hazelwood, Missouri |
Associate Process Engineer | Durham, North Carolina |
Electrical Engineer II | Salt Lake City, Utah |
Engineering Co-op | |
Industrialization Engineer | Lombard, Illinois |
Manufacturing Engineer | Philadelphia, Pennsylvania |
Manufacturing Engineer IV | Salt Lake City, Utah |
Manufacturing Maintenance Tech 2 - Night Shift | Durham, North Carolina |
Manufacturing Maintenance Tech 3: Electrical - Night Shift | Durham, North Carolina |
Mechanical Engineer III | Salt Lake City, Utah |
Principal Engineer, Reagent Engineering | Hazelwood, Missouri |
Process Engineer | Durham, North Carolina |
QA Engineering Co-op | Philadelphia, Pennsylvania |
Sr Project Manager - Manufacturing and Operations | San Jose, California |
Systems Engineer | Hazelwood, Missouri |
Validation and Verification Engineer | Hazelwood, Missouri |
Validation Specialist 2 | Lombard, Illinois |
Manufacturing
Scientific/R&D
Clinical Affairs Lab Tech I | Hazelwood, Missouri |
Data Scientist II – System Validation Analysis | Salt Lake City, Utah |
Data Scientist III – Product Research Analysis | Salt Lake City, Utah |
Field Medical Director | United States |
Firmware Engineer III | Salt Lake City, Utah |
Lead Data Scientist | San Jose, California |
Lead Engineer - Instrumentation and Algorithms | Durham, North Carolina |
Postmarket Surveillance Specialist II | Salt Lake City, Utah |
Project Coordinator II, Clinical Affairs Program Management | Hazelwood, Missouri |
Scientist | San Jose, California |
Scientist | San Jose, California |
Scientist II | Salt Lake City, Utah |
Senior Firmware Engineer | Hazelwood, Missouri |
Senior Project Manager, Clinical Affairs Microbiology Portfolio | Hazelwood, Missouri |
Sr Manager, RA Life Cycle Management | |
Sr. Scientist | San Jose, California |
Software/IT
IS Portfolio Manager - Finance | Salt Lake City, Utah |
Visual Analytics Implementation Specialist | United States |
What I Like About BioFire
“ By far, the best benefits of any company I’ve seen in my 40 year career. ”
Roy I. - Engineering
“ This is a high-intensity laid back environment. ”
Cory E. - Engineering
“ Flexible hours, getting every other Friday off and just shy of 4 weeks of vacation is spoiling me. ”
Andrea S. - Software Development
“ I enjoy being part of the growth we’re experiencing. ”
Jeff N. - Biochemistry
“ Best team environment-Ever! ”
Tony M. - Materials Management
“ A fun culture that fosters innovation and risk taking. ”
Wade S. - Sales & Marketing
“ Working for a company that is always striving to provide the best solutions for the industry. It doesn’t feel like we are here to make a buck, we come to work each day to save lives and to make the world a better place. ”
Sarah Z. - Marketing
“ Generous 401k plan with no vesting period! ”
Sheila P. - Finance
“ I think my absolute favorite thing about this company is that we are still growing and making new things, and the passion and excitement that goes along with it. ”
Mary J. - Instrument Manufacturing
“ Education. I like that BioFire will invest in my future with the tuition reimbursement program, and not only that, I am given the flexibility to do what I need to get it done. ”
James O. - Information Technology
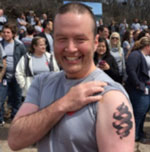
“ A great thing about BioFire is that no one freaked out about my new tattoo! ”
Paul M. - Regulatory Affairs
BioFire Diagnostics, LLC. provides equal employment opportunities (EEO) to all employees and applicants for employment without regard to race, color, religion, gender, sexual orientation, gender identity or expression, national origin, age, disability, genetic information, marital status, amnesty, sex, creed, citizenship status, or status as a covered veteran in accordance with applicable federal, state and local laws. BioFire Diagnostics, LLC. complies with applicable state and local laws governing non-discrimination in employment in every location in which the company has facilities. This policy applies to all terms and conditions of employment, including, but not limited to, hiring, placement, promotion, termination, layoff, recall, transfer, leaves of absence, compensation, and training. Our Affirmative Action Program is available for inspection by any applicant or employee by contacting the Human Resources office Monday through Friday, 8:00 am – 5:00 pm MST. To view additional information regarding our commitment to equal opportunity, please visit the OFCCP website.