Discover Domtar
Domtar makes products that people around the world rely on every day.
As part of the Paper Excellence Group we design, manufacture, market and distribute a wide variety of communication, specialty and packaging papers, market pulp and airlaid nonwovens.
For nearly two centuries, we have built a legacy in our industry by being agile and innovative. We are leaders in caring for the environment and operating sustainably. We invest for the long term in our people, and we enable and encourage them to succeed.
To learn more, visit www.domtar.com.
At Domtar, you will find:
-
Careers for contributors who adapt to change and grow with enthusiasm and expertise. Our company's entrepreneurial spirit honors hard work and ingenuity with exciting opportunities for advancement.
-
Colleagues who have compassion and respect for one another, actively caring for each other's safety and the environment. We welcome and value people with a variety of experiences, perspectives and cultures.
-
Causes to embrace, related to our products that enhance literacy, health and wellness, and sustainability. We are proud of what we do and how we do it.
Benefits
We want you to excel in your career at Domtar, which is why we offer competitive benefits that enhance your quality of life, help you invest in your future, and protect you and your family's health and welfare. These include:
-
Paid Vacation
-
Education Reimbursement
-
Health and Welfare Benefits
-
401K/Retirement Savings, Company Match and Employer Contribution
-
Income / Financial Protection
-
Parental Leave
*Benefits vary depending on division and location.
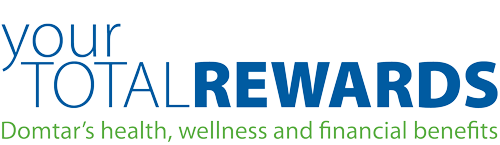
At Domtar, compensation is more than just a paycheck. It's the combination of vacation days, incentive plans, group benefits, savings and retirement programs, as well as wellness, scholarship, employee assistance programs (EAP) and more.
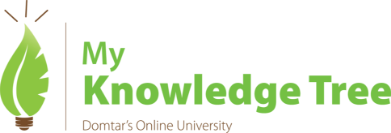
From nationally-recognized professional certifications to personal development, Domtar's online university, My Knowledge Tree, allows employees to learn new or enhance existing skills on demand. Whether completing an Individual Development Plan at work or browsing on a tablet at home, thousands of courses, videos, books, and job aids are just a click away.
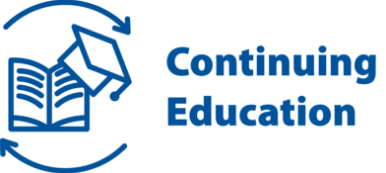
Domtar offers many formal and informal learning opportunities for employees. Tuition reimbursement and on-site, certified professional education courses help employees participate in academic training even while working. Our orientation and on-the-job training programs give employees the skills and knowledge needed to contribute from day one and to succeed when they move into new positions. Our Growing Leaders program is preparing the next generation of manufacturing leaders by passing on the skills and experience from our current leaders.
Our Company
Pulp, Paper & Packaging
Corporate
As part of the Paper Excellence Group, we design, manufacture, market and distribute a wide variety of fiber-based products including communication, specialty and packaging papers, market pulp and airlaid nonwovens.
We have shown agility in re-purposing facilities to align with market demands. Our roadmap for the future allows us to look forward with confidence about our product mix.
We make our products at manufacturing and converting facilities in the U.S. and Canada, with a focus on safety, quality and sustainability.
Our Corporate employees provide internal support services to the main business functions of the organization, including Human Resources, Corporate Communications, Information Technology, Finance, Audit, Sustainability, Legal and Government Affairs.
Domtar’s principal executive office is in Fort Mill, South Carolina and Domtar is part of the Paper Excellence group of companies.
Ariva is a Domtar owned and operated distribution company that offers a spectrum of high quality paper, packaging and industrial supplies to help businesses communicate, collaborate, and compete more effectively.
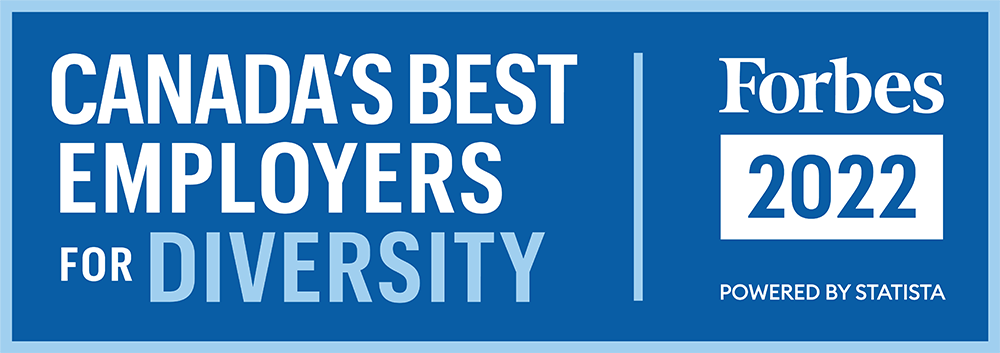
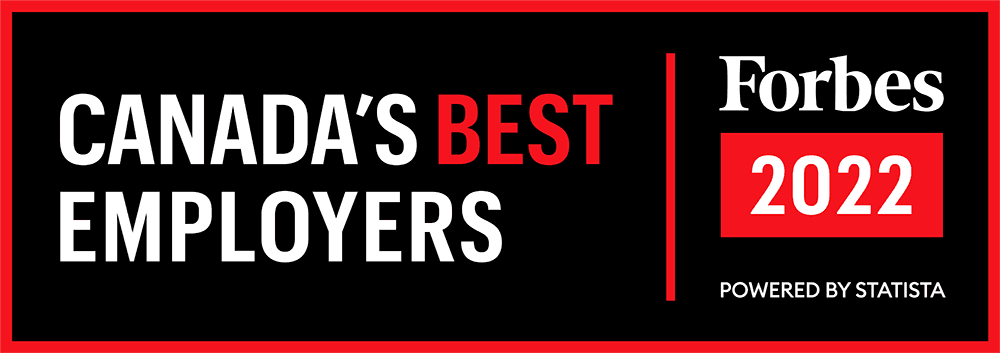
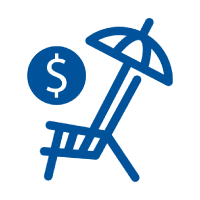
Domtar offers a competitive paid annual vacation plan based on continuous years of service.
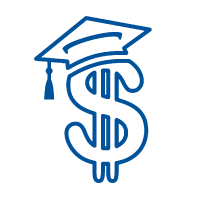
Domtar encourages and supports the personal and professional development of our employees. Our education reimbursement program has been established to help develop our employees' growth in current or future positions.

We are committed to delivering health and well-being programs that support our employees in taking action and adopting healthy behaviors. We aim to improve the physical, psychological and financial health of our employees through education and activities that support healthy lifestyles.
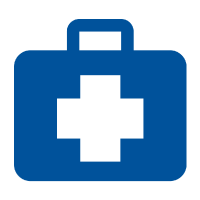
Domtar provides a competitive medical plan that varies based on location.
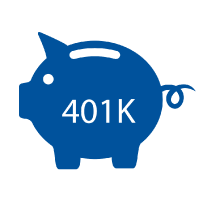
Domtar has a 401k plan that includes company match and an additional employer contribution.
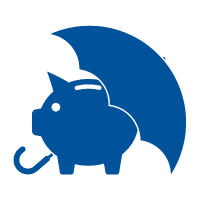
Domtar offers disability coverage that helps you meet your expenses when you cannot work because of a qualifying disability. Domtar provides income replacement protection under short-term disability and long-term disability at no cost to employees.

In order to help mothers and fathers bond with their newborn or adopted child, we offer parental leave to eligible employees.
Follow Domtar
We’re proud to share our story. Visit our online resources below and learn more about who we are, how we work, and what we’re doing next.