The job listing no longer exists.
Our purpose statement is:
"To boldly change our energy future"
We’re working to do that every day at Franklin Energy. We serve utilities, municipalities, businesses, and customers across the country to lower their carbon emissions and create a healthier environment for future generations. Join us!
Explore Our OpportunitiesBenefits
Remote work opportunities
Our employee base spans the entire country with options for many positions to be remote.
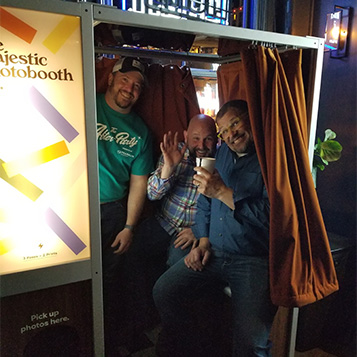
Mind and body wellness program
We offer a variety of wellness activities, recognition programs, and lunch-and-learns.
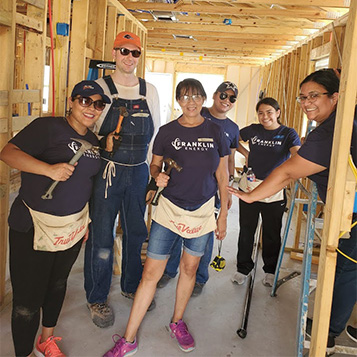
Business casual work environment
We’re not the stodgy corporate type, and we don’t expect you to be, either.

Performance bonus opportunities
We believe in rewarding a job well-done.

Training programs, both internally and externally
We’ll support and work with you on driving your development and helping you reach your next milestone.

Flexibility around a 40-hour work week
If traditional workday hours don’t always work for you, don’t sweat it!
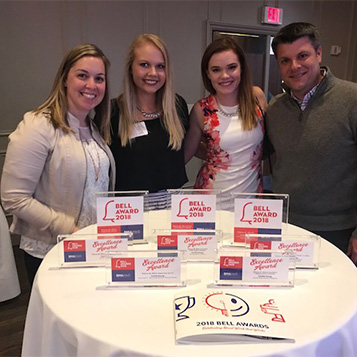
Dental, health, and vision coverage
We offer healthcare options for all employees.

401(K) with company match
We’ll help you start saving for your future, today.

Paid parental leave
We offer paid parental leave for parents to focus on family.

Company-paid volunteer hours
Giving back to our local communities (and our environment) is engrained in who we are.

Insurance options
We offer short- and long-term disability as well as basic life insurance.
Life at Franklin Energy
We live our core values, and we have fun while we’re doing it.
We inspire.
We empower every customer with smart, affordable, carbon-reducing energy solutions.
We innovate.
We introduce new ideas to build strong communities and local economies free from the effects of climate change.
We are inclusive.
We work in a safe, diverse, and collaborative culture to solve the complexity of long-term energy management and equity.

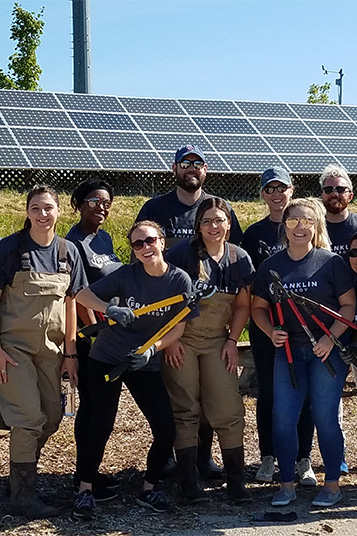

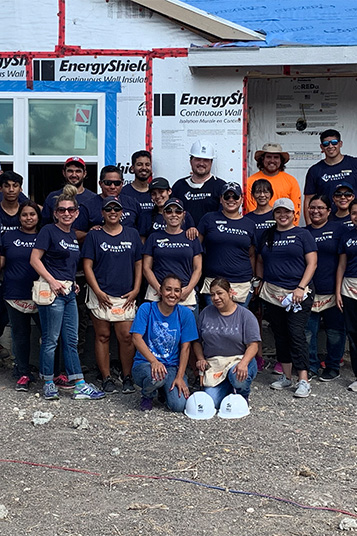

Our Experts
Excellence grows from the inside out. Franklin Energy experts live our purpose each day—to boldly change our energy future.
A Franklin Energy expert is:

Confident, but not arrogant.

Efficient, without cutting corners. We always put safety first.

Responsible, accountable, and willing to learn.

Respectful to clients, customers, each other, and even competitors.

Experienced, but flexible to adapt to the ever-changing industry.

Supportive of the success and safety of our clients and coworkers.
Our Recruitment Process
Review
We review applications to screen for a variety of criteria.
Introductory Call
Candidates are invited to an introductory call with one of our recruiters.
Interview
We conduct interviews to get to know each candidate better and ensure the potential role is the right fit for both the team and the individual.
Offer
We make an offer to the candidate we feel is best for the role.
Welcome to the team!
How Can You Join Our Team of Experts?
If Franklin Energy sounds like the right fit for you, browse our job listings to see how you can join our team of experts.